Sacramento Crossdock Warehousing - An Overview
Wiki Article
The Facts About Sacramento Crossdock Revealed
Table of ContentsGetting My Sacramento Crossdock Warehousing To WorkCrossdock Warehouse for Dummies9 Easy Facts About Crossdock Warehouse ExplainedFascination About Sacramento WarehouseSacramento Cross Dock Fundamentals Explained

As a part of SCM, efficient inventory administration may lead to a stronger supply chain. An additional factor excellent warehousing is necessary to SCM is that it offers a means for companies to make sure the accessibility of the right products at the correct place whenever the moment is right. It raises the energy value of the goods that method - Sacramento Crossdock Warehousing.
Consumers anticipate to know when approximately their acquisitions will certainly be supplied after an order is positioned. The understanding concerning the delivery time enhances their self-confidence. Several of them pay faster because of this. Obviously, they end up being more reluctant when unpredictability exists around the timely distribution of products. Nowadays, distribution speed appears to be among the considerable variables that consumers think about when choosing an item and determining whether to wage the acquisition.
The Basic Principles Of Sacramento Warehouse
A considerable factor to purchase developing a storage facility is the several known economic advantages that come with it. Not only the enhanced performance of the supply chain but additionally the warehouse's storage space capacity as well as just how it acts as a main location for your items add to its financial advantages.These things can be seen or realised with debt consolidation and build-up operations. Right here's a more detailed look at how debt consolidation and build-up can help lower costs: With debt consolidation procedures, there's no requirement to deliver products individually from numerous sources because they might be delivered to your storage facility as stocks. As soon as an order is placed, you or your team can load and also deliver the item out from there.
Not only that, but excellent warehousing additionally boosts client service as well as supplies financial advantages. Every one of these things could result in greater revenue and improved business earnings.
See This Report on Crossdock Warehouse
Individuals who fill products into a warehouse and also others ("pickers") that fill orders in a real circulation center, plus those that handle the facility and procedure. Access to cost-effective transport to bring products in or move them out as orders are fulfilled.They also need to make certain that products are kept in a safe as well as safe and secure manner. In retail shops, things are stored as well as arranged in a warehouse as well as delivered to consumers or other stores.
Warehousing ideal technique is to make use of RF Scanners, or equivalent innovations, to more boost supply precision as well as actual time stock monitoring. Very closely linked with Getting, Putaway is the last of incoming handling. Putaway is the process of physically, and systematically, placing products into their appropriate last storage space places (Sacramento Crossdock). Team chooses Item to putaway from Putaway Staging area, Typically Pallets or Carts with Product ready to be putaway, Using RF Scanner, determine what cart/pallet/job you are putting away and check one-of-a-kind identifier to begin Putaway, Picker travels to area to place product for storage space, find out here Suitable best in course systems inform staff where to put item, but several warehouses still have team location product where they recognize there is vacant area (with some criteria applied)RF Check Item being putaway as well as Location where the Item is putaway, Continue process (go to area as well as area supply) until whole order, pallet, cart, and so on is total Weight and dimensions of product/pallet being putaway, Stowability of Item (ie breakable, stackable, etc)Purchase quantity (best-sellers put close vs NOT far away)Amount received, Worth of product, Select Kind of Item (single choice, set choice, view cluster choice, area choice, etc) Accurate Putaway is crucial in the warehouse procedure, making sure that Product can be quickly located specifically when it is needed.
7 Simple Techniques For Sacramento Cross Dock
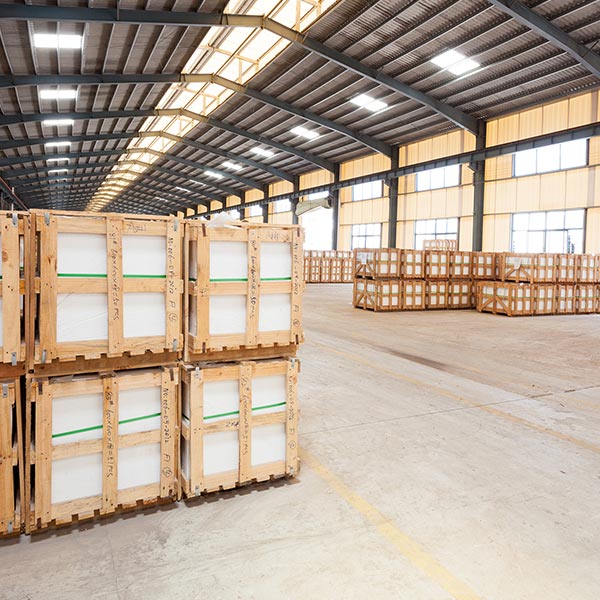
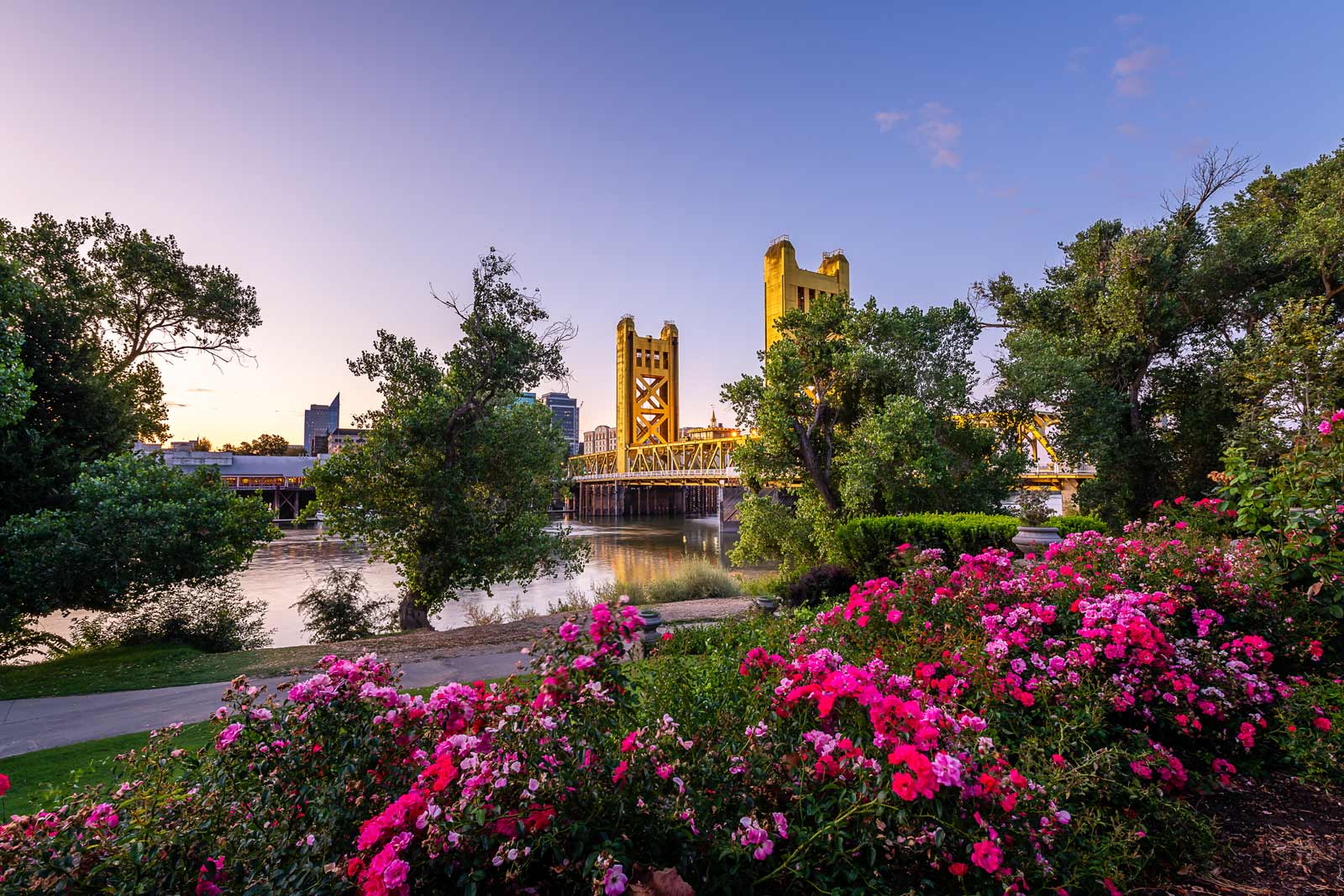
Similar to how Obtaining lays the structure for a precise stock, Selecting lays the structure to precisely satisfy a customer's order. Selecting is the process of celebration Products to satisfy a client's order demand. Picker is assigned Select(s)There are lots of choose techniques, each operation is distinct in what is most reliable for their requirements, Area choosing, set picking, solitary order selecting, wave picking, and a lot more, Using RF Scanner, or comparable, begin choosing by entering the One-of-a-kind Choose Identifier (set #, Order #, SO #, Choose #, various other reference)Picker is transmitted with the Choose Path (ideally based upon optimization logic) to meet the Select, scanning Products as well as Locations as they progress, Selected products might be placed in totes, pallets, carts, shelf, and so on during pick, Totally selected orders provided to following phase of process, Selected orders may be provided to a High quality Control area, Packing/Shipping area, or directly to outgoing staging (if pick to classify operation) depending upon procedure Limitations/abilities of current Stockroom Management System (WMS)Volume of Orders # of Item Lines per Order, Kind of storage space media (shelving vs racking vs ground pallet storage)What the Packing and also Shipping Refine looks like (carefully intertwined to Selecting)Item need added focus throughout packing? Transportation Management System (TMS) capable of supplying delivery tags prior to things are selected? Much much more! Stockroom Layout Selecting must be done properly, with quality assurance steps in location post-picking, to accomplish client order gratification precision near 100%.
So if throughout shipping the weight is not within the defined resistance range, after that the user will certainly be prompted to take activity, Dimension anchor resistance check during Shipping, Comparable to Weight tolerance based on system measurement information Packing and Delivery is a significant focus of stockrooms, as it commonly becomes a traffic jam because Order Handling Time have to be as short as possible to satisfy client assumptions.
Do NOT sacrifice high quality! It is vital to note, relying on the storage facility operation Packing may be combined with the Picking procedure. Inventory Control is an integral part of all warehouse procedures. You can assure the supply at the storehouse is accurate and up-to-date with a well specified Supply Control procedure.
The Sacramento Crossdock Warehousing PDFs
Cycle Matters as well as Full Supply Counts are devices connected with preserving Supply Control. Cycle Counts take place continually while regular operations continue, yet Full Inventory Counts take place regularly and need all product activity to stop until a complete accurate matter is finished. Shutdown all supply activities, completing all Item Activities in the Storehouse (physically and also methodically)Make certain all inbound and also outgoing orders that have been literally processed, have actually likewise been processed in WMSBreak warehouse group into teams to count (in some cases 1 individual team okay)Groups are designated locations to count Assign small-medium areas to count, after that teams sign in for more locations as needed, Groups count assigned locations, recording matters of product per place, Teams usually utilizing RF Scanners to videotape counts, Or else need to do paper-based which is difficult to attain a Blind Matter, Team reports back when completed as well as receive next Count Job, After areas are Counted, the Manager/Lead examines all Variations, Supervisor assigns various Team to state the troubled Products and/or Locations, If 2nd group counts like 1st team, make supply change to match physical count.Report this wiki page